Projecten die maar weinigen durven te proberen
Speciale bestellingen maken deel uit van de dagelijkse werkzaamheden van Elektro-Projekt Mittweida GmbH. Toch komt een maatwerkklus als deze schakelkastcontainer voor een staalfabriek Hubert Timmel niet dagelijks tegen.
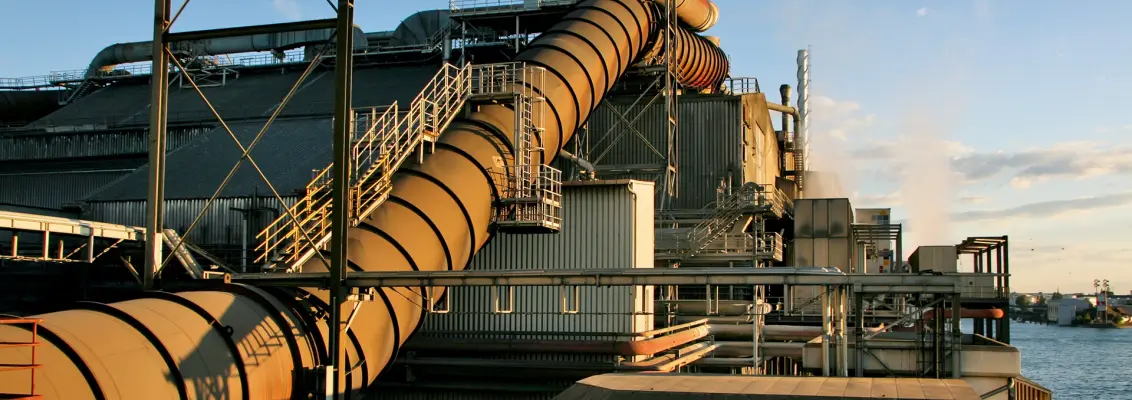
Met een breedte van 3 meter, een hoogte van 3,6 meter en een lengte van 8 meter (10 voet breed, 12 voet hoog en 26 voet lang), werd de grijze container gebouwd in de productieruimte van Elektro-Projekt Mittweida GmbH (EPM) in Frankenberg, Saksen, en zal binnenkort zijn laatste thuis vinden in Kehl, aan de Rijn in Duitsland. Directeur Hubert Timmel loopt via een van de verzonken deuren de gewone container binnen. Mike Grambow, area sales manager bij HELUKABEL, volgt hem. Hij is best opgewonden om te zien hoe de kabels zijn aangebracht. “Als leverancier krijg ik deze kans niet vaak. Vandaag ga ik echter een live testrun bijwonen.“ Zeven solide metalen kasten - allemaal volgepropt met voorschakelapparatuur - vullen de linkerhelft van de container. “De container is voor Badischen Stahlwerke GmbH (Baden Steelworks, BSW) in Kehl. De inhoud omvat een middenspanningsomvormer en het regelsysteem voor een afzuigventilator”, zegt Timmel, terwijl hij een van de schakelkastdeuren opent. Achter de deur bevindt zich een goed gesorteerde reeks kabels, connectoren en printplaten. “Naast de gebruikelijke kabels zoals de middenspanningskabels zijn er servokabels voor de ventilatormotor. Deze stuurkabel loopt buiten de container en is dus UV-bestendig. Het verbindt de voorschakelapparatuur van de container met de staalfabriek. En tot slot zijn er alle afzonderlijke kernen, die de componenten in de schakelkast met elkaar verbinden”, legt Grambow uit. Direct naast de open schakelkast bevindt zich het hart van de machine: een middenspannings-frequentieomvormer. “Dit is een custom feature die we in samenwerking met Siemens hebben ontwikkeld. We hebben met elke kubieke millimeter geworsteld om de converter in de container te krijgen”, legt Timmel uit. De converter regelt de ventilatorsnelheid die de uitlaatgassen van de smeltovens door een gigantische pijp met een diameter van 3 meter blaast. “Tot nu toe had de ventilator slechts twee standen: aan en uit. BSW wilde hier verandering in brengen en heeft een refit laten uitvoeren.” De technologie van EPM analyseert de gemeten gegevens van de molen en past de ventilatorsnelheid dienovereenkomstig aan. "De meet- en datatransmissiekabels geven de informatie door van de molen naar de computer in de container", zegt Grambow, wijzend op de relevante kabelstrengen. “Op deze manier kan BSW zoveel energie besparen”, benadrukt Timmel.
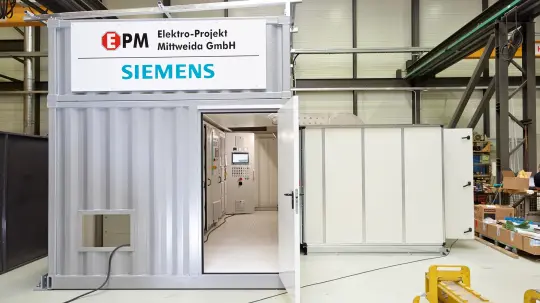
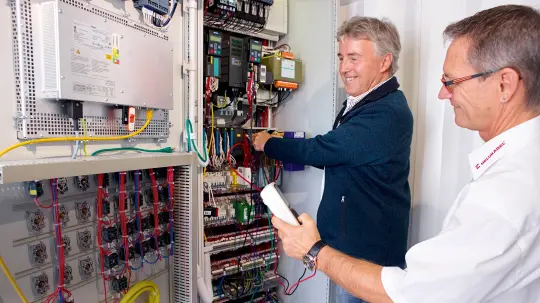
EEN SPECIALE BESTELLING
Aangepaste taken zoals deze zijn eigenlijk niets bijzonders voor EPM. Uitzonderlijke oplossingen maken deel uit van het bedrijfsmodel van het bedrijf. “We doen dingen die maar weinigen durven te proberen.” Met ‘dingen’ bedoelt hij schakel- en schakelkasten voor klanten in de automobiel- en industriële sector en fabrikanten van machines voor maatwerk. “We beschouwen onszelf als een totaalleverancier. Ons servicebereik strekt zich uit van hardware- en softwareplanning tot verzending en inbedrijfstelling.“ EPM is zeer succesvol geweest met dit concept. Toen Timmel het bedrijf begin jaren 90 oprichtte, had hij 16 werknemers - nu heeft hij er 130. Desalniettemin is de bestelling van Baden Steelworks geen gewone, zelfs niet voor Hubert Timmel. “Voor dit project was het essentieel dat alles op rolletjes liep, zowel technisch als qua tijd.” Een staalfabriek lijkt misschien veerkrachtig en sterk, maar is eigenlijk heel storingsgevoelig. Je kunt het niet zomaar uitschakelen. Als de ovens zijn afgekoeld duurt het dagen voordat ze weer op bedrijfstemperatuur zijn. Er moest een oplossing worden gevonden die de werkzaamheden niet onderbrak. Gecompliceerde refits ter plaatse waren uitgesloten, wat betekende dat het enige alternatief een kant-en-klare containeroplossing was. “BSW trok twee dagen uit voor de inbedrijfstelling.” Om zich aan de deadline te houden, had Hubert Timmel betrouwbare leveranciers nodig. EPM was de hoofdaannemer voor BSW. Maximaal zes verschillende bedrijven moesten nauwkeurig worden geïntegreerd in het strakke tijdschema. “We werken al vele jaren samen met HELUKABEL, dus we wisten dat we konden vertrouwen op stipte levering. “Terwijl Timmel en Grambow de container verlaten, herinnert Timmel zich de geslaagde generale repetitie. Tijdens uitgebreide tests van de afgelopen weken is elke functie meerdere keren gesimuleerd. Aan het einde werd de technologie geïnspecteerd en geaccepteerd door vertegenwoordigers van BSW. Nu moet het zich in de praktijk bewijzen. Timmel loopt weg van Grambow en legt uit dat de container morgen aan zijn reis begint; een reis van 550 kilometer (342 mijl), 10 uur op een dieplader.
MONTAGE BIJ DAGERAAD
Een dag later, om vijf uur 's ochtends, staat Timmel op het terrein van de staalfabriek met een team van vier medewerkers die met hem meereisden. De meeste mensen slapen op dit moment nog, maar Timmel en zijn team zijn klaarwakker. Ze kijken met spanning toe hoe de 12-tons container onder leiding van Timmel voorzichtig door een kraan wordt neergelaten op een aangepast platform dat zo'n 15 meter boven de grond is gebouwd. In vergelijking met de imposante staalfabriek lijkt de container op een klein bouwblok.
"Zo, dat is de eerste etappe die is voltooid", zegt Timmel, die meteen met zijn team aan de slag gaat. Aan het einde van de tweede montagedag is er een collectieve zucht van verlichting. Zij deden het! De techniek loopt gesmeerd. Maar mocht er een onderdeel kapot gaan, dan staat er een vervanging klaar. “De bovenkant van de container kan eenvoudig worden verwijderd zonder stroom- of besturingskabels los te koppelen. Zelfs grotere onderdelen kunnen worden vervangen zonder het bedrijf voor een langere tijd te onderbreken.“