Q&A With HELU: Oil & Chemical Resistance
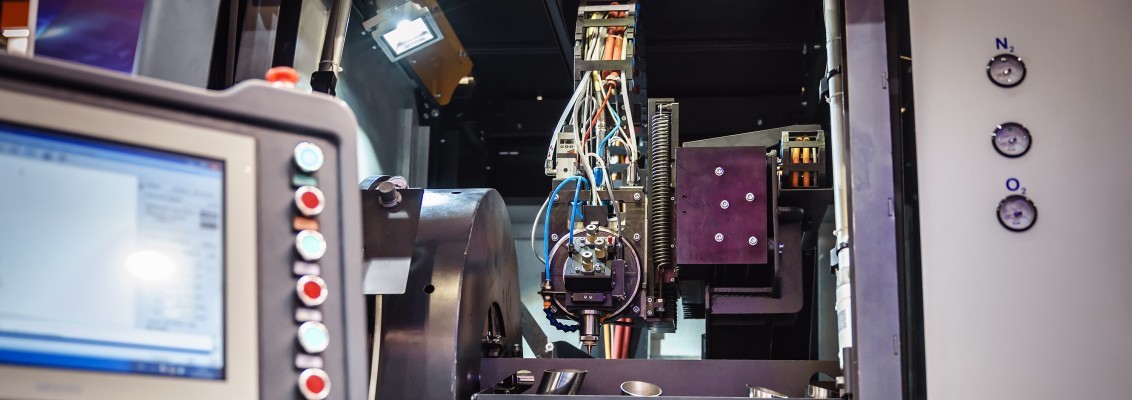
Not all environments where you find cables and wires are the same. Factors to consider for cables in an IT cabinet or routed through an office building are not the same as the demands on cables that are located in an industrial setting. Harsh chemicals, oils, and other lubricants are just a few of the challenges that cables providing power or transmitting data must withstand in industrial environments to keep operations online. Regional Sales Manager David Newton dives into detail and provides answers to some of the questions he hears in the field about industrial cables and their resistance to substances found in the industrial sector.
Q: What industries require cables to be resistant to organic and inorganic substances?
A: Many industrial markets need to be mindful of the environmental impacts placed on the cables and wires they use. Machine tools, chemical processing plants, food and beverage processing, manufacturing and assembly, oil and gas, and renewable energy – solar and wind, are just a few that expose cables and wires to very harsh chemicals, cleaning agents, solvents, oils, greases and other lubricants that will leave the equipment they support useless if the cables aren’t protected or capable of resisting these organic and inorganic substances. When compared to the overall market, the industrial segment requires cables and wires to be constructed using some of the most technically advanced compounds to resist the chemicals and oils found in industrial environments, while still maintaining their flexibility, UV and flame resistance.
Q: What negative effects can oils, solvents and chemicals have on cable jacket performance?
A: Did you know that an ingredient in manufacturing rubber is oil? And if you park or store your car tire in a puddle of oil it will cause the tire to lose its protective properties and begin to warp or ripple. Much the same, certain harsh chemicals and oils will cause a jacket to degrade the longer it is exposed to these substances. Depending on the substance the jacket is exposed to causes the plasticizers added during jacket compound manufacturing to either be displaced by or absorb the substance they are in contact with.
UL, CSA and VDE are just a few of the independent testing agencies that provide guidelines for cables to make sure they function properly in applications where harsh chemicals and oils are present. Some common oil tests used in UL 62, UL 1277, MTW and Oil Res I and II, test a cable’s resistance by completely immersing it in oil at various temperatures and lengths of time. These tests are used for cables to receive several UL-specific approvals such as machine tool wire (MTW), tray cable (TC), and service cordage (ST, SO and DLO). Cable jacket compounds that meet these approvals include PVC, PVC/nylon, TPE or rubber compounds.
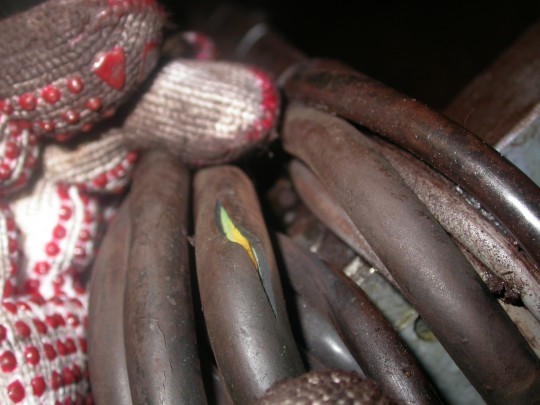
Q: What are some visual indicators that a cable’s jacket or insulation is being compromised by oil and chemical exposure?
A: There are four key indicators that the outer jacket is being affected by oil and chemical exposure that should cause the user to start considering a replacement during scheduled maintenance to avoid an unexpected failure and subsequent unplanned downtime. These indicators are:
Cracking – Oil or chemical exposure has resulted in the complete removal of plasticizers. This hardens the insulation and jacket, which makes them brittle and more susceptible to cracking/breaking.
Swelling – Oil or chemical exposure has resulted in the migration of the oils into the plasticizers. This results innoticeable diameter increases in the insulation and jacket.
Melting – Oil or chemical exposure has been absorbed and combined with the plasticizer. This softens and makes the compound more elastic than intended.
Discoloring – Oil or chemical exposure has resulted in the diffusion of the plasticizers along with colorant from the insulation and jacket.
Q: What other factors can exacerbate oil and chemical exposure on the life span of a cable’s jacket and insulation?
A: Cables used in industrial environments expose cables to different types of environmental and mechanical conditions that can further speed up the degradation of the cable’s jacket when oils and chemicals are added to the equation. From an environmental perspective, temperature and exposure to UV light tend to be the main influencers. There are oil exposure certification tests that must be passed to receive specific approvals that give engineers operating parameters for how a cable will perform at certain temperatures over varying time frames. The same can be said for cables that are exposed to the sun in outdoor environments. UV-rated cables tend to withstand the long term effects of constant sun exposure than non-UV-rated cables, e.g. they don’t dry out and become brittle as quickly thereby exposing the inner conductors or the actual copper and/or aluminum strands. When it comes to mechanical influences, any movements that cause cables to break down either by abrasion or twisting forces can allow oils and chemicals to seep into areas that they should not, which opens the cable up to potential failures if not addressed quickly.
Q: What jacket options are available that can stand up to the effects of oils and chemicals?
A: There are many types of thermoplastics used to resist oil and chemicals, including such options as polyvinyl chloride (PVC), polyurethane (PUR), fluorinated ethylene propylene (FEP), and thermoplastic elastomers (TPE), to name a few. Choosing the right material – PVC, FEP, TPE, PUR, rubber or blends – is important to eliminate downtime on a factory floor or in the field.
In the industrial machine tool industry, as an example, PUR cables used to provide motor power and feedback often times can be immersed in oil and synthetic-based cutting fluids around the clock. Their performance has led them to be the standard in the machine tool market for more than a century.
However, PVC-based cables have become a growing business for cable manufacturers due to the advancements in compound additives and blending (different types of plastics) to achieve various performance characteristics. Recent changes in UL certification, i.e., the expanded use of tray cable with exposed run (TC-ER) approvals, have opened up more applications for these cables on the industrial floor.
Knowing how, where and what the cable will be exposed to will aid you and your cable supplier in selecting the proper jacket material that is best for your specific application.